If there is one term that tends to make many jewellers, setters and polishers nervous, it is the term CAD, which stands for “Computer Aided Design”. This technique appeared in the jewellery sector at the very beginning of the 2000s, but it is only in the last ten years that it has been used intensively in the workshops and design offices. But why is there so much tension about a method that seems interesting? Quite simply because of the lack of practical training of computer graphic designers who have joined our sector without having practised jewellery making at the bench. Because what looks good on a screen is not always beautiful when it comes to scraping and assembly.
With this in mind, I went to meet Max Mazlo, a jeweller and above all a freelance computer graphics designer in the 9th arrondissement of Paris, to understand how CAD can be a help and how it should be practised to make things work perfectly.
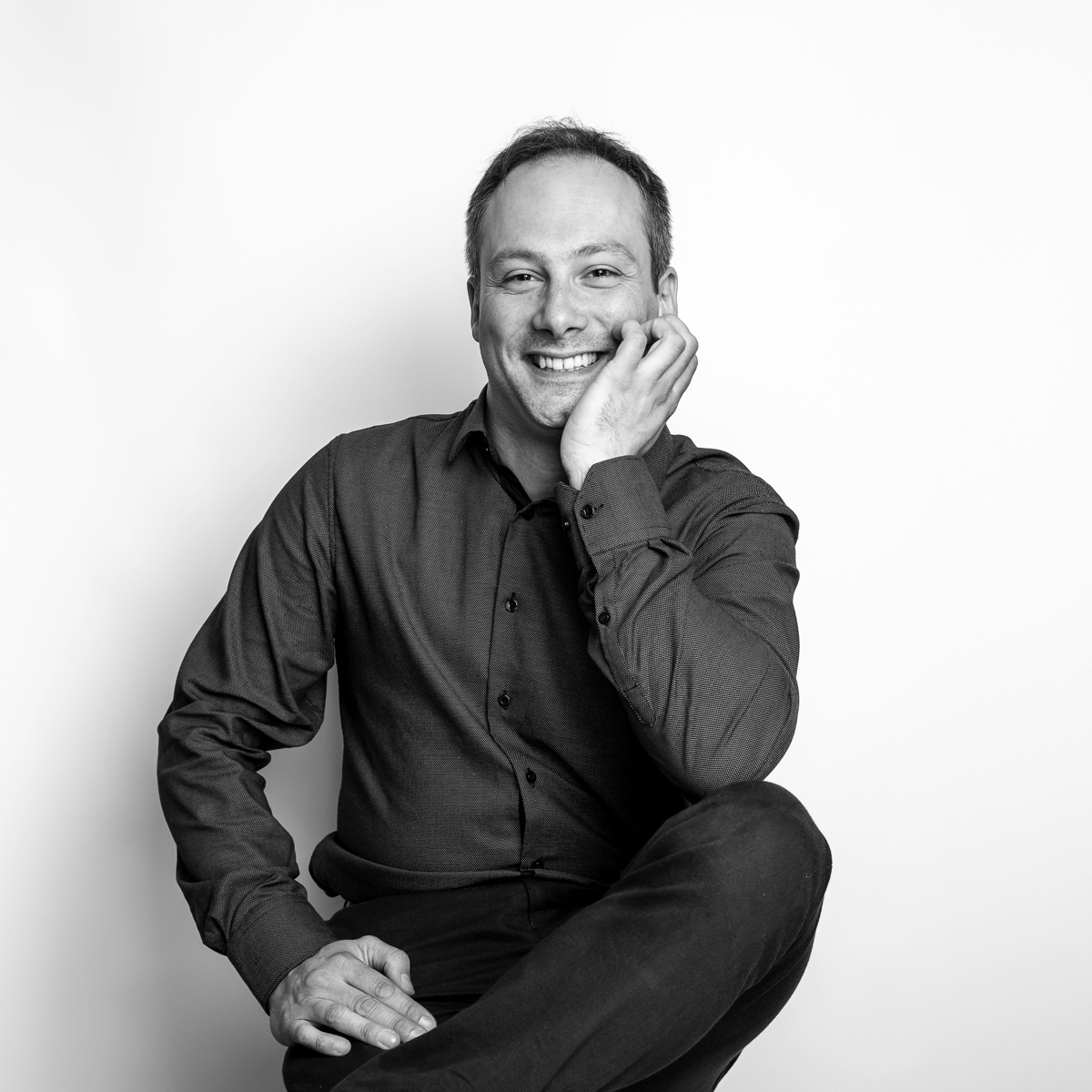
Max Mazlo
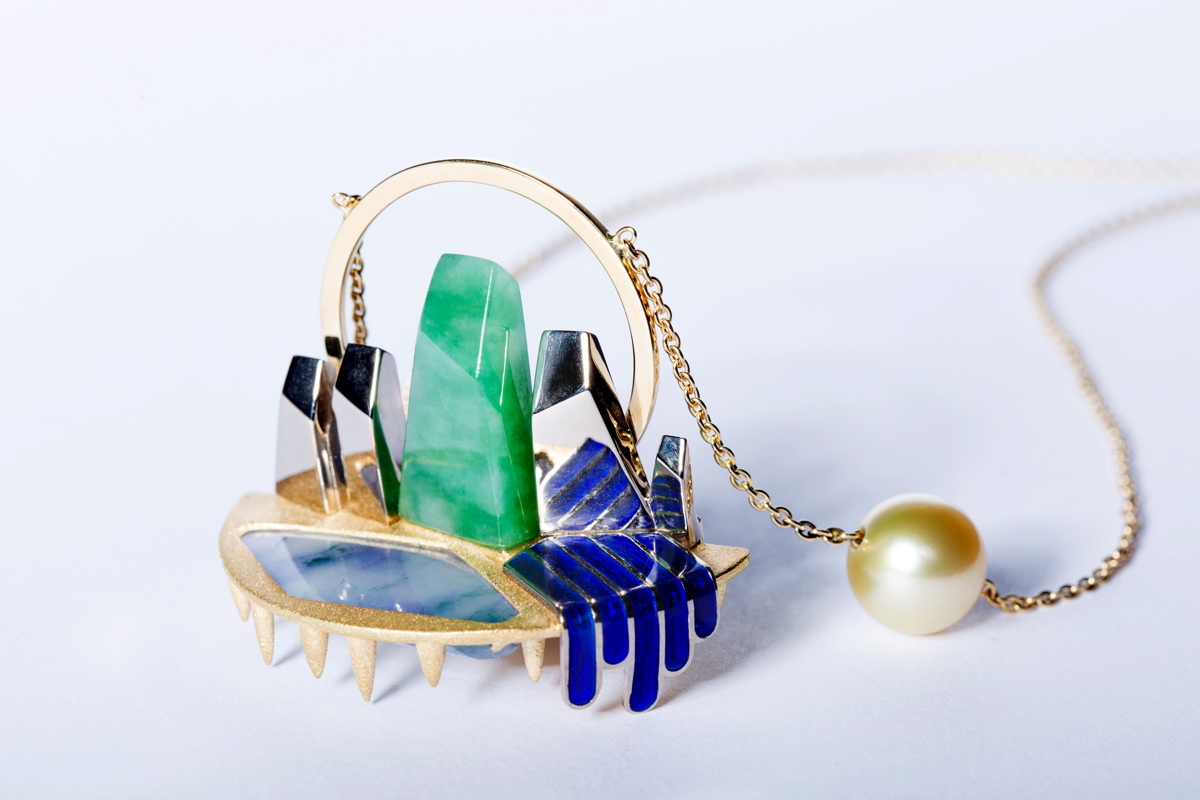
Gold, jade, enamel and pearl pendant. Private collection. Photo: Max Mazlo
Before setting up his own business, Max first followed a practical training in jewellery and worked for many years with his father: Robert Mazlo. In 1997, he joined the Nicolas Flamel high school, at the time a leading training centre for jewellery. Today, the school no longer exists as such but has merged with the École Boulle, which has seen the creation of a jewellery training department. He first passed his CAP and then a BMA. He also tried his hand at setting for a short year. Not to become a gem setter, but to better understand how it works and the technical requirements that a jeweller must respect when making a piece. It is also during his studies that he approaches in a partial way the work on the computer because this one makes a timid appearance in the schools. This was only the beginning of a movement that would have a lasting impact on the sector.
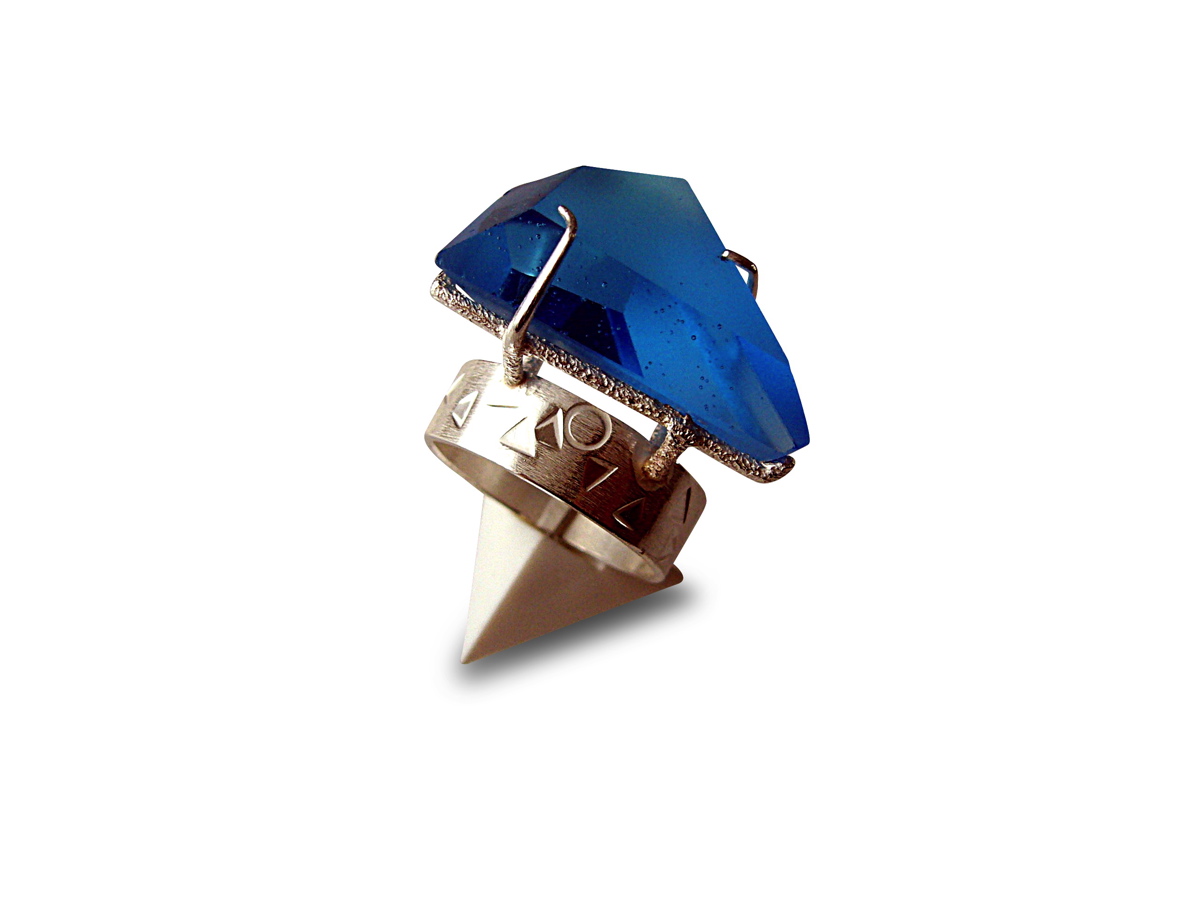
Silver ring and stained glass window from Chartres. Private collection. Photo: Max Mazlo
After Flamel, he joined the AFEDAP to develop his creative desires and to get away from the technical side. Following this, he joined his father’s company where he stayed for almost four years from 2004 to 2008. He describes this period as“a time dedicated mainly to creativity“. Although technique is important to the Mazlo family, it must not be separated from invention and imagination. A piece must be correctly executed but it must also tell stories. He experimented with many different materials: gemstones, Chartres stained glass, etc. During all these years, he continues to work on CAD software, he follows training courses, learns about new processes and continues to improve his practice of these new tools which, when he leaves the family workshop, are now perfectly implanted in the manufacturing process in jewellery. In 2008, he joined a high jewellery workshop for a few months to do in-house CAD development and then decided to set up his own business at the very beginning of 2009. At the same time, he also became a trainer for Rhino 3D, a major supplier of software for the jewellery industry. This is how MaxM, his company dedicated to 3D design and printing, was born.
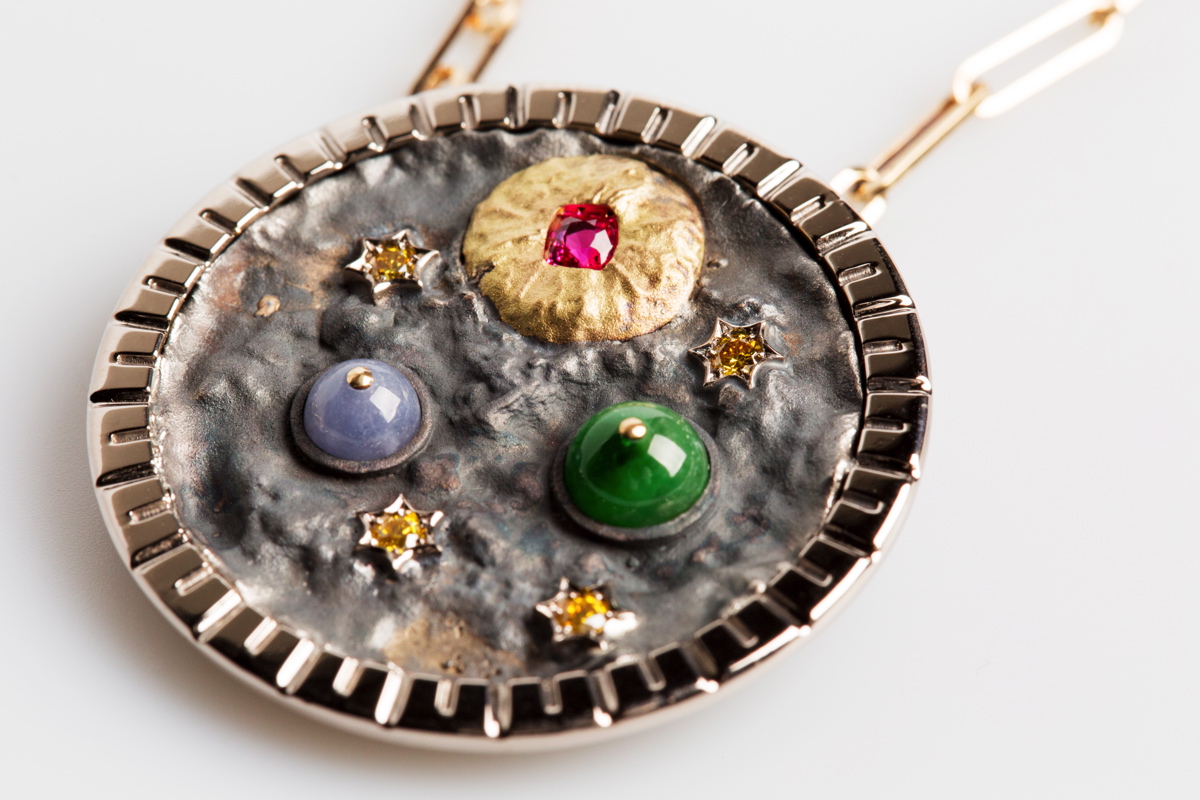
White and yellow gold pendant set with a surround of black and white diamonds, a peridot, an amethyst and a Tahitian pearl. Private collection. Photo: Max Mazlo
“3D combines challenges and technicality. But in jewellery making, it requires a good base at the workbench to practice it properly. Without that, you end up with the kind of tension we know about: poorly designed pieces, adjustments that don’t work, miscalculated castings, time that shouldn’t be wasted.”
Max Mazlo
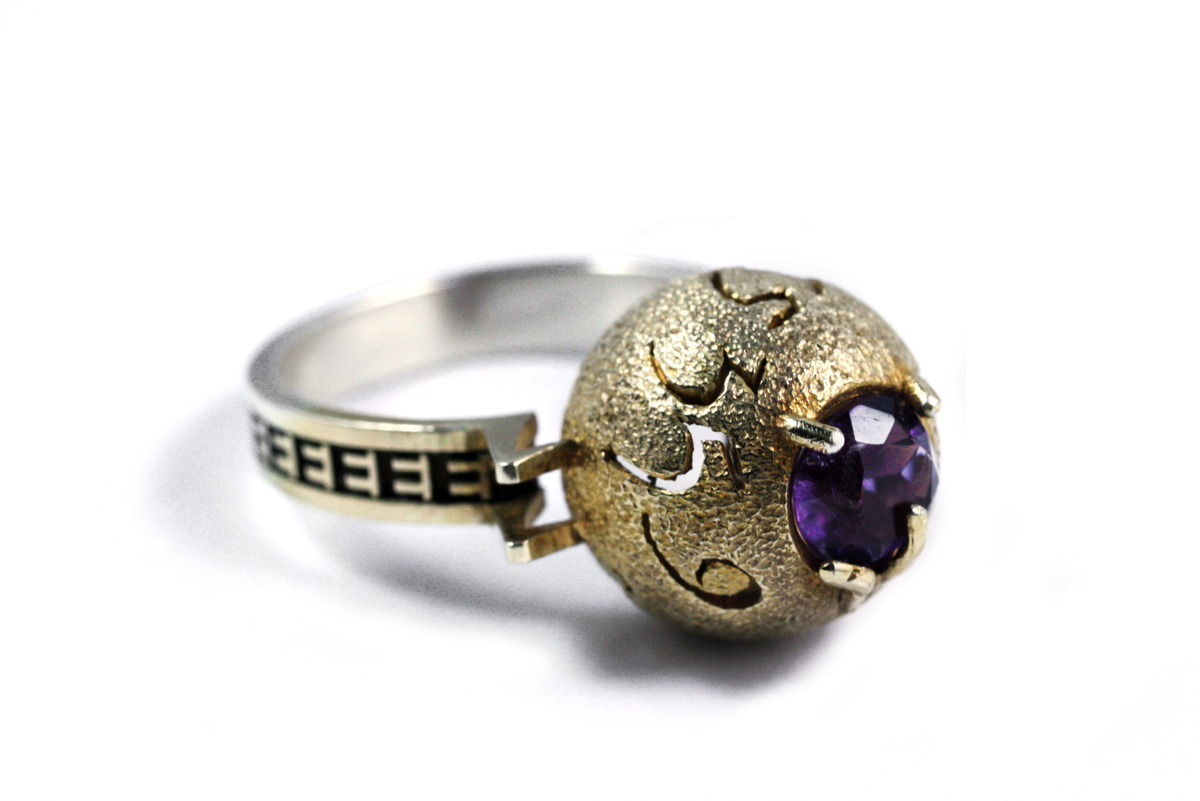
Ring in polished/brushed silver and hammered vermeil, set with an amethyst. Limited series of ten. Photo: Max Mazlo
In addition to his expertise in modelling and his work for his jewellery and design clients, Max also initiates creative work for a few privileged clients, in Europe but also in Asia and more particularly in Japan. He does not describe himself as an artist but as a technician and finds in this creative practice a different way of doing his job. Convinced also that 3D is not always the perfect solution, he does not hesitate to work by hand when this is the only way to achieve the desired result. His personal work mixes gold, titanium, diamonds, jade… He follows his own inspiration. When asked if he will ever design a complete collection, he believes it is possible. The only thing left to do is to find the common thread of this collection, but also the time, because in addition to his business, he is also a teacher at the Académie des Métiers d’Art where he passes on 3D with his own way of doing things well so that it is no longer a source of tension for many craftsmen.
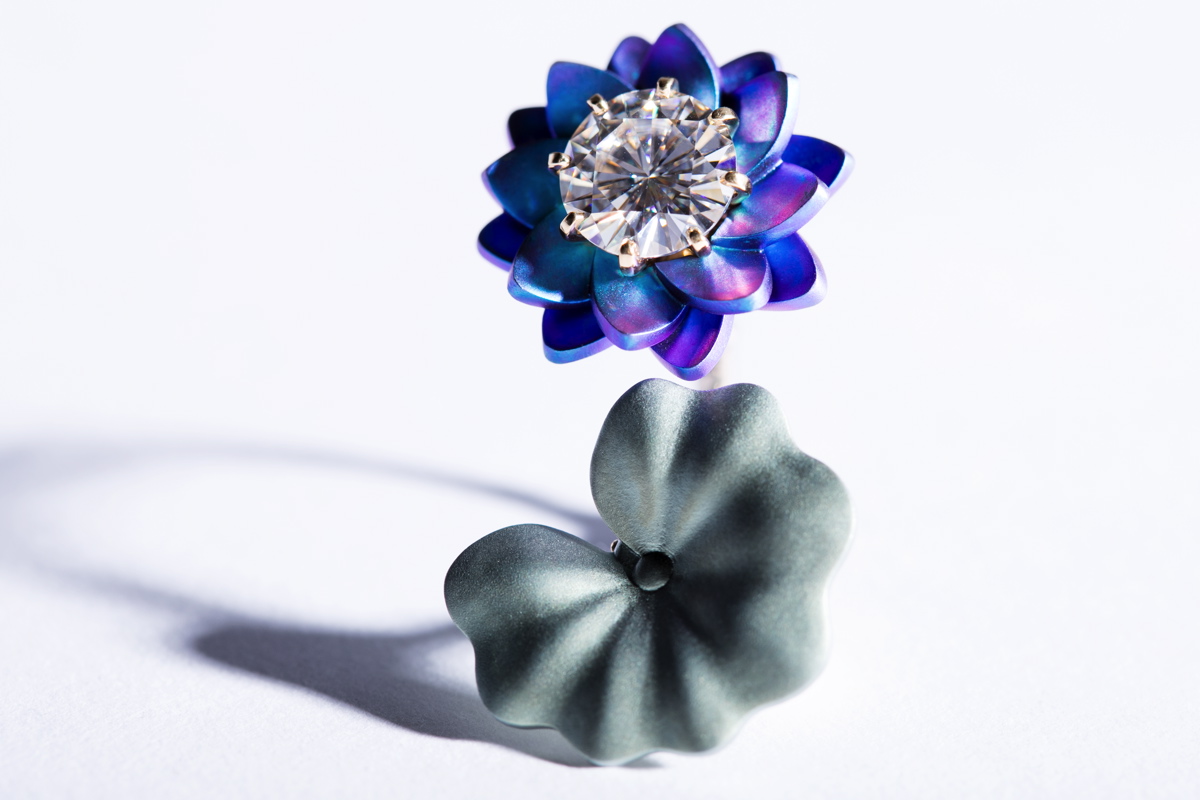
Gold, titanium and diamond ring. Photo: Max Mazlo
Today, modern computer techniques are well present in our profession, they continue to evolve and developers and design offices are going further and further. The latest collection from Boucheron, for example, uses CT scans to capture all the nuances of the flowers and plants in “Nature Triumphante”. From now on, you know that 3D can only be good for you. On the ultimate condition that it is practiced by jewellery professionals and also in a reasonable use. In any case, you also know who to contact!
See you soon!
*****
Max Mazlo – MaxM
32 rue des Victoires, 75009 Paris
+33 (0) 1 77 18 31 76